Sydney Business InsightsSydney Business Insights,
text
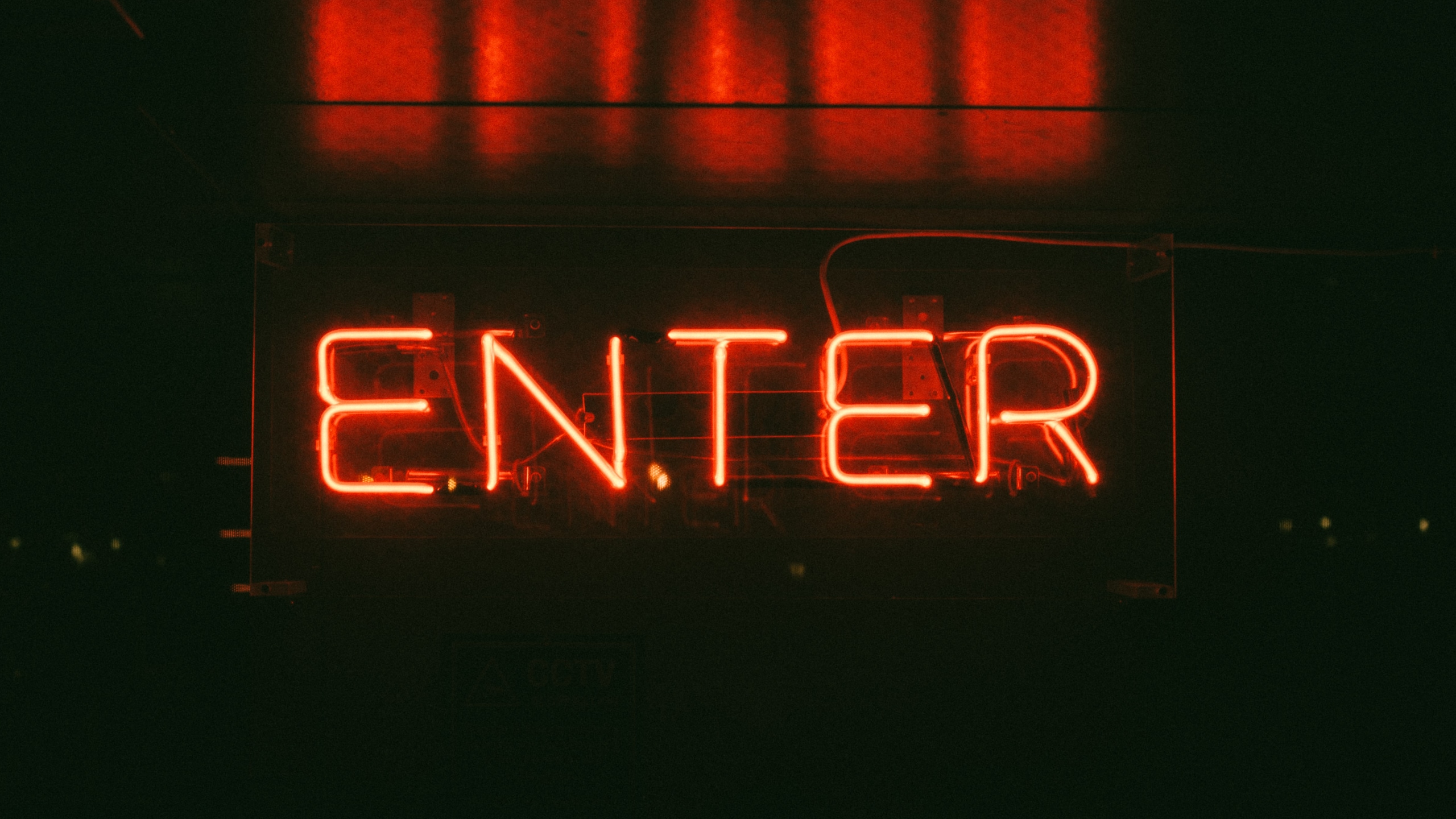
Neon supply lines. A rare story.
The towns of Mariupol and Odesa have become infamous for the destruction wrecked upon their people and buildings in the Russian invasion of Ukraine.
These two cities are also home to the Cryoin factory in Odesa and the Ingas plant in Mariupol which between them produce more than 50% of the world’s supply of high-quality neon gas.
Neon gas is the element that gave the neon sign both its name and its distinctive orange fluoro illumination.
Neon is also an essential ingredient in the production of semiconductor computer chips – those wafer-thin silicon slices that are essential to the operation of electronics, cars, computers, phones, new airplanes, dishwashers and many other everyday items.
Neon in a nutshell
The Ukrainian factories specialise in producing the purified version of neon needed to precision-guide the lasers that turn silicon into the tiny circuits that make computers work. The neon controls the wavelength of light emitted by the lasers, necessary because the chips are so small and intricate.
Neon is a by-product of steel production and Cryoin and Ingas previously had good access to the raw ingredient via the steel factories scattered throughout the former Soviet Union. This supply has also been impacted by the war.
Supply lines, a global story
The Russian invasion have forced both factories to close, impacting customers in Taiwan, Korea, China, the USA and Germany.
This will further exacerbate the worldwide shortage of computer chips which have been under pressure since COVID-19 drove up demand for electronic goods such as computers, cell phones and cars.
The ‘hidden’ neon connection to these everyday necessities peels back the layers of supply chain complexity that goes into producing some of the products we take for granted. It’s a story that also resonates in the tale of the construction of lithium-ion batteries. These batteries are an essential part of the renewable resource future life-cycle, present in electric vehicles, phones, laptops and solar power storage. And they need some of the world’s rarest minerals, cobalt and lithium with limited supply options. Cobalt is mainly found in the Congo, lithium in Australia and Chile.
While we may be familiar with the economics and the supply chains of things like oil or coal markets the move to more sophisticated products such as computer chips and batteries means that we’re now faced with a technology that is incredibly complex and requires an almost inscrutable web of resources.
System shock
Modern production process for complex products is spread throughout the world. Companies source components from specialised third-party manufacturers because up to now it has been efficient and cost effective to do so. This distributed production practice flourished in the relatively peaceful post WWII period, during which the world also escaped global shocks such as pandemics.
What the pandemic and now the ongoing war in Ukraine – and let’s include the growing threat of climate change – makes clear, is that this system is also precarious, and that a complication in the production of even the most basic component or ingredient can jeopardise the world’s access to all sorts of tech. Neon is just the latest example, and it’s unlikely to be the last.
Image: Clem Onojeghuo
Sydney Business Insights is a University of Sydney Business School initiative aiming to provide the business community and public, including our students, alumni and partners with a deeper understanding of major issues and trends around the future of business.
Share
We believe in open and honest access to knowledge. We use a Creative Commons Attribution NoDerivatives licence for our articles and podcasts, so you can republish them for free, online or in print.